Dall’officina tradizionale alla fabbrica intelligente: come abbiamo digitalizzato un’azienda del settore automotive
Il mercato automobilistico è sempre più competitivo e richiede una flessibilità produttiva senza precedenti. La personalizzazione dei prodotti e la riduzione dei lotti di produzione sono diventate la norma. Per far fronte a queste sfide, le aziende manifatturiere devono adottare soluzioni innovative che permettano loro di ottimizzare i processi e aumentare l’efficienza.
Un caso di successo nel cuore dell’industria automobilistica
Sintesi Software è stata chiamata a supportare una media impresa del settore automotive, con l’obiettivo di trasformare la sua produzione tradizionale in una fabbrica intelligente. L’azienda, con oltre 150 dipendenti, produceva componenti meccanici e si trovava ad affrontare una serie di sfide:
- Aumento della domanda di personalizzazione: I clienti richiedevano prodotti sempre più personalizzati, con lotti di produzione sempre più piccoli.
- Macchinari eterogenei: L’azienda disponeva di un parco macchine eterogeneo, con modelli di diverse marche e età , rendendo difficile l’integrazione di nuove tecnologie.
- Necessità di ottimizzare i processi: L’azienda sentiva l’esigenza di migliorare l’efficienza produttiva e ridurre i tempi di fermo macchina.
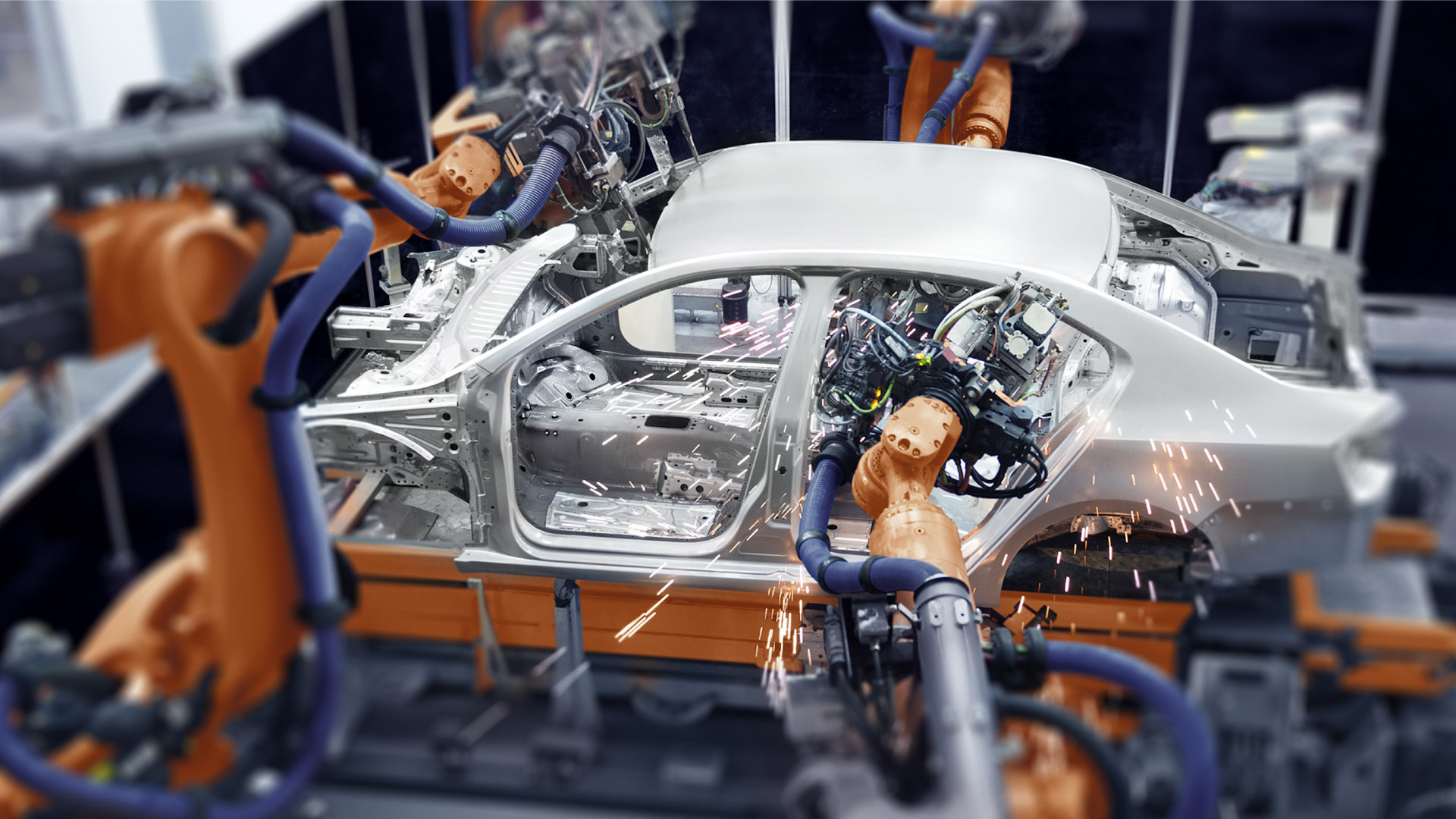
La nostra soluzione: una fabbrica connessa e intelligente
Per affrontare queste sfide, abbiamo implementato una soluzione completa di Industria 4.0, applicando i seguenti step:Â
1. Mappatura delle macchine presenti nei reparti dell’Azienda
I nostri tecnici hanno da subito mappato il reparto e monitorato i macchinari tramite sistemi di smokeping.
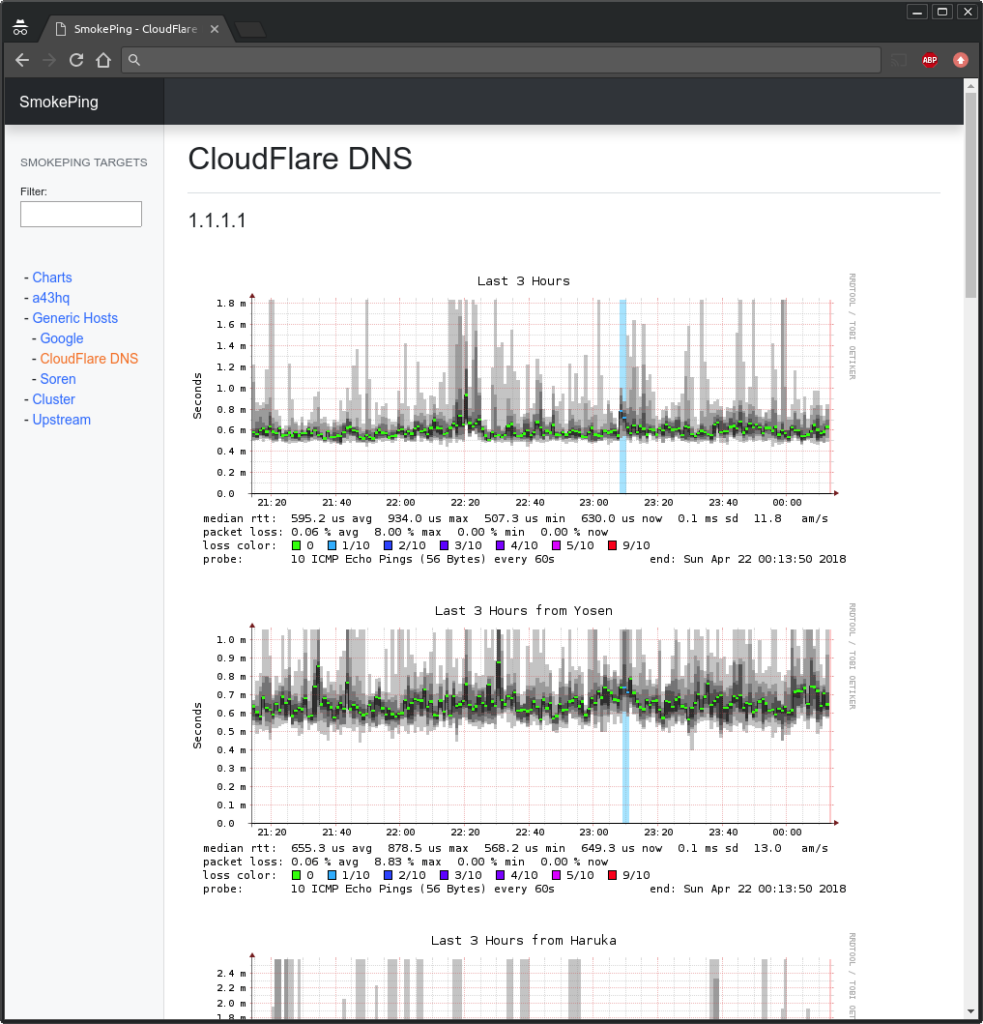
Da subito è emerso che l’oggetto della connessione erano macchinari moderni già predisposti per l’interfacciamento con sistemi 4.0 con diversi protocolli coinvolti. Inoltre c’erano anche macchinari Legacy (modelli di diverse marche e età ) di diverse marche e modelli che non erano nativamente progettati per la connettività .Â
2. Installazione di Sensori IoT
Per monitorare i macchinari Legacy i tecnici hanno installato direttamente sulle macchine sensori per rilevare parametri come temperatura, vibrazione, pezzi prodotti, etc..
3. Configurazione protocolli di colloquio
A seguito del monitoraggio sono stati definiti i protocolli da implementare per collegare le macchine del nostro Cliente:
- OPCUA
- MT-connect
- Modbus
4. Definizione dei flussi dati
Sono stati definiti i flussi da implementare tra il nostro software gestionale di produzione t/clock con le singole macchine presenti nei reparti interessati.
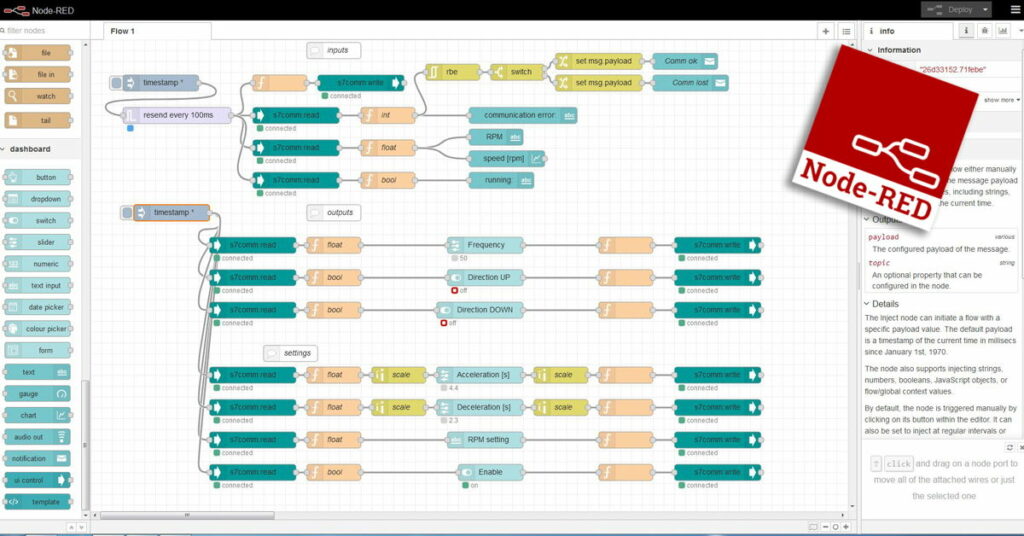
5. Attivazione concentratore 4.0
Mappati e definiti i flussi tra il software gestionale e le macchine, abbiamo trasferito i dati sulla nostra piattaforma Industry 4.0. La nostra piattaforma è un concentratore che riceve i dati dal software di produzione t/clock e li invia alle macchine; allo stesso tempo il concentratore interroga periodicamente i macchinari per acquisire tutti i loro dati necessari per il monitoraggio delle lavorazioni. Tutti i dati acquisiti vengono inviati al nostro programma di produzione t/clock per consentire la consuntivazione automatica delle fasi di lavoro.
6. Interfaccia con t/clock e il software per gestione della manutenzione e MES:
Abbiamo poi interfacciato t/clock con il nostro CMMS inviando I dati rilevati dai macchinari al nostro software di produzione t/clock. In t/clock si trovano tutte le fasi di lavoro relative agli ordini di lavoro in essere. L’acquisizione di questi dati consente l’aggiornamento automatico degli avanzamenti di fase (pezzi prodotti, tempi di lavorazione, anomalie, …)
7. Attivazione Piattaforma di Monitoraggio dati t/monitor
Abbiamo poi transitato i dati rilevati dalle macchine anche sulla piattaforma di analisi dati t/monitor; trattasi di una piattaforma cloud per l’analisi dei dati raccolti, con dashboard personalizzate per il monitoraggio degli stati macchina e delle loro performance.
Seguono alcuni grafici di analisi disponibili:
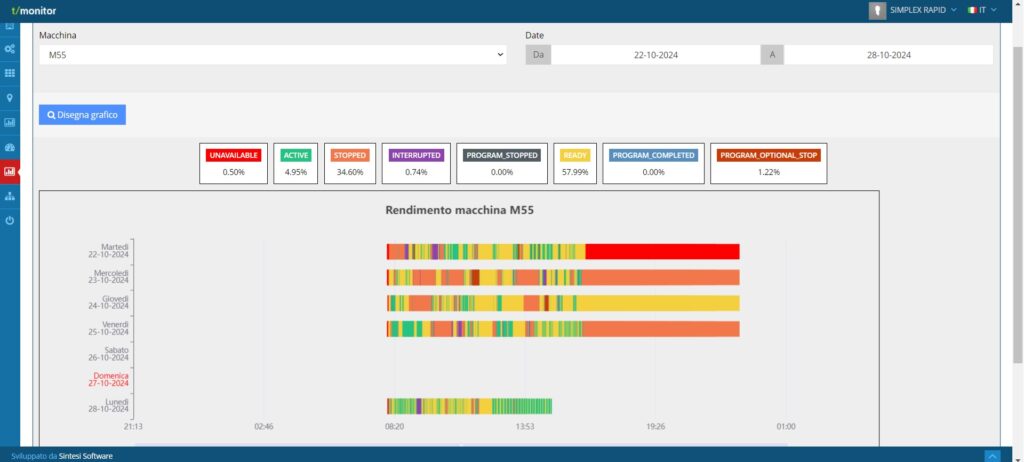
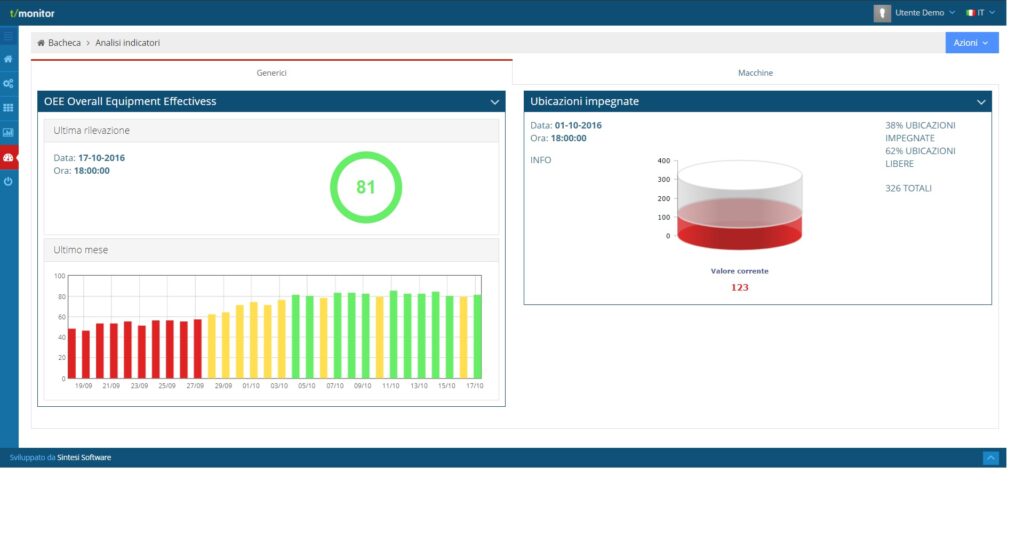
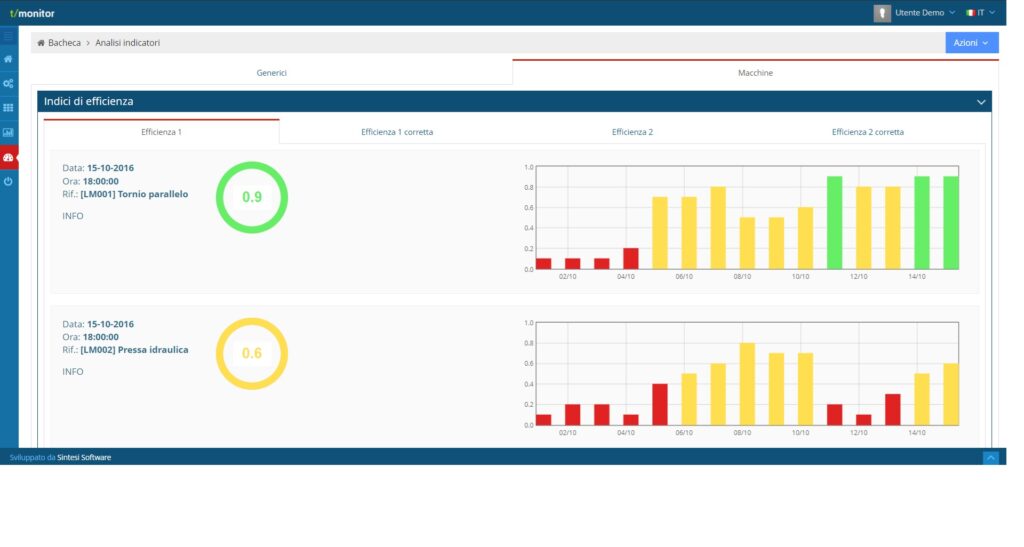
8. Sistema di Manutenzione Predittiva:Â
I dati rilevati dai macchinari sono stati poi inviati anche al nostro software t/tools dedicato alla gestione della manutenzione degli impianti.
Grazie all’implementazione di algoritmi di machine learning le manutenzioni preventive vengono aggiornate e corrette per poter fornire analisi volte a prevedere guasti e ottimizzare i tempi di intervento.
9. Formazione e Supporto
Al termine dell’implementazione del sistema abbiamo tenuto dei corsi di formazione per il personale sull’uso della nuova piattaforma. Inoltre continuiamo a fornire supporto tecnico continuo.
Più smart, più efficiente: il viaggio di un’azienda verso l’Industria 4.0
Grazie all’implementazione della nostra soluzione, l’azienda ha ottenuto i seguenti risultati:
- Aumento dell’efficienza produttiva: Riduzione dei tempi di fermo macchina e ottimizzazione dei processi produttivi.
- Miglioramento della qualità dei prodotti: Maggiore controllo sulla qualità grazie alla raccolta e all’analisi dei dati di produzione.
- Maggiore flessibilità produttiva: Capacità di rispondere rapidamente alle richieste di personalizzazione dei clienti.
- Riduzione dei costi di manutenzione: Grazie alla manutenzione predittiva.
Â
Questo caso di successo dimostra come le soluzioni di Industria 4.0 possano trasformare anche le aziende di medie dimensioni, rendendole più competitive e flessibili. Grazie alla nostra esperienza e alle nostre tecnologie, siamo in grado di supportare le aziende manifatturiere nel loro percorso di digitalizzazione. Se anche tu vuoi scoprire una soluzione ad hoc per digitalizzare la tua azienda non esitare a contattarci!Â